熊維舟,何建軍,張 煒,任延杰
(長沙理工大學(xué)能源與動(dòng)力工程學(xué)院,長沙 410114)
摘 要:采用腐蝕動(dòng)力學(xué)分析法,研究了12Cr1MoV 低合金鋼在高溫(600,700 ℃)70%NaClG30%KCl、50%NaClG50%KCl、30%NaClG70%KCl(質(zhì)量分?jǐn)?shù))混合鹽中的熱腐蝕行為,觀察了表面及截面腐蝕形貌,分析了腐蝕產(chǎn)物成分并研究了其腐蝕機(jī)制.結(jié)果表明:12Cr1MoV 鋼在高溫混合鹽中會(huì)發(fā)生嚴(yán)重的表面與內(nèi)部腐蝕,其內(nèi)部產(chǎn)生的氯氣是導(dǎo)致裂紋與孔洞等缺陷萌生和擴(kuò)展的主要原因;隨混合鹽中 KCl含量的增多和溫度的升高,試樣的腐蝕速率明顯增大;較高含量的 KCl使鋼內(nèi)部由沿晶腐蝕轉(zhuǎn)變?yōu)檎w性侵蝕.
關(guān)鍵詞:12Cr1MoV 鋼;堿金屬混合氯鹽;熱腐蝕;微觀結(jié)構(gòu)
中圖分類號(hào):TG178 文獻(xiàn)標(biāo)志碼:A 文章編號(hào):1000G3738(2017)04G0058G06
HotCorrosionBehaviorof12Cr1MoVSteelinHighTemperatureMixedAlkaliChlorideSalt
XIONG WeiGzhou,HEJianGjun,ZHANG Wei,RENYanGjie
(SchoolofEnergyandPowerEngineering,ChangshaUniversityofScience& Technology,Changsha410114,China)
Abstract:Hotcorrosionbehaviorof12Cr1MoVlow alloysteelin mixedsaltsof70% NaClG30% KCl,
50%NaClG50%KCl,30%NaClG70%KCl(massfraction)at600 ℃ and700 ℃ wasstudiedbythecorrosionkinetic
method,respectively.Thecorrosionmorphologyatthesurfaceandcrosssectionwasobserved,thecompositionof
thecorrosionproducts wasanalyzedandthecorrosion mechanism wasinvestigated.Theresultsshowthatthe
12Cr1MoVsteelwascorrodedseriouslyatthesurfaceandinthesubstrateinthehightemperaturemixedsalts.The
producedCl2insidethesteelwasthemainreasonfortheinitiationandpropagationofdefectstructuresuchascracks
andpores.WiththeincreaseofKClcontentin mixedsaltsandofthetemperature,thecorrosionrateofsample
increasedrapidly.Thecorrosionmodeinthesubstratechangedfromintergranularcorrosiontointegralcorrosiondue
totherelativelyhighcontentofKCl.
Keywords:12Cr1MoVsteel;mixedalkalichloridesalt;hotcorrosion;microstructure
0 引 言
12Cr1MoV 鋼具有高強(qiáng)度、良好的抗氧化和耐腐蝕性能[1-2],被廣泛用于制造生物質(zhì)電廠鍋爐過熱器熱管.生物質(zhì)中含有大量的鉀、鈉、氯元素,在燃燒時(shí)所產(chǎn)生的堿金屬氯鹽結(jié)渣使該鋼的工作環(huán)境相當(dāng)惡 劣,容 易 導(dǎo) 致 熱 腐 蝕 問 題,對(duì) 鋼 材 造 成 破壞[3-4].現(xiàn)有研究表明,高溫氯鹽能使金屬晶界層中大量的鐵和鉻元素由基體向腐蝕介質(zhì)中遷移,并
加速合金內(nèi)部的腐蝕[5-6].此外,高含量的 NaCl還會(huì)加深合金內(nèi)部的熱腐蝕程度[7],對(duì)其使用性能有很大的影響.
耐熱鋼的熱腐蝕問題一直是合金材料耐腐蝕研究的重點(diǎn)[8].由于不同生物質(zhì)燃燒時(shí)在熱管表面形成的堿金屬鹽結(jié)渣成分復(fù)雜,而目前國內(nèi)外傳統(tǒng)研究又主要集中在某一特定成分對(duì)材料的腐蝕上,因此有必要研究不同成分對(duì)材料的腐蝕作用并分析其機(jī)理.
此 外,堿金屬鹽結(jié)渣也會(huì)導(dǎo)致過熱器熱管的局部過熱,對(duì)材料進(jìn)行高溫腐蝕研究也顯得尤為重要.因此,作者以不同配比的 NaClGKCl混合堿金屬氯鹽為腐蝕介質(zhì),在不同溫度下對(duì)12Cr1MoV鋼進(jìn)行了腐蝕試驗(yàn),研究了該鋼的腐蝕行為并分析了其腐蝕機(jī)理.
1 試樣制備與試驗(yàn)方法
1.1 試樣制備
試驗(yàn)材料為某生物質(zhì)電廠燃燒鍋爐過熱器熱管用12Cr1MoV鋼,該鋼的熱處理工藝為1180℃×2h空冷+1050℃×4h空冷+800℃×16h空冷;其主要化學(xué)成分如表1所示.
采用線切割從試驗(yàn)鋼上切出尺寸為 9 mm×9mm×9mm 的試樣,用360# ,800# ,1000# ,1500# ,2000# 水磨砂紙逐級(jí)打磨,同時(shí)用 M1.5的鉆石拋光膏拋光至無明顯劃痕,然后依次使用蒸餾水、丙酮、
無水乙醇清洗并干燥.按 30%NaClG70%KCl、50%NaClG50%KCl和70%NaClG30%KCl(均為質(zhì)量分?jǐn)?shù),下同)分別稱取NaCl和 KCl,配制成總質(zhì)量為50g的混合堿金屬鹽,置于氧化鋁陶瓷坩堝中,在馬弗爐中于200℃干燥12h.然后將試樣放入混合堿金屬鹽中進(jìn)行熱腐蝕試驗(yàn),腐蝕溫度分別為600,700℃,腐蝕時(shí)間分別為12,24,48,60h.腐蝕試驗(yàn)結(jié)束后,用蒸餾水清洗試樣表面的氯鹽,風(fēng)干待用.
1.2 試驗(yàn)方法
使用 AUX120型電子分析天平測腐蝕前后試樣的質(zhì)量,將腐蝕后與腐蝕前試樣的質(zhì)量差記為試樣的腐蝕 質(zhì) 量 變 化.采 用 JSMG6360LV 型 掃 描 電 鏡(SEM)觀察試樣表面腐蝕形貌.用1500# 水磨砂紙打磨并拋光試樣截面,并用4%(體積分?jǐn)?shù))硝酸酒精溶液腐蝕后觀察截面形貌,并測量未脫落腐蝕產(chǎn)物的厚度和除去表面氧化膜后腐蝕層的平均厚度,利用附帶的能譜儀(EDS)分析截面微區(qū)的元素組成.
2 試驗(yàn)結(jié)果與討論
2.1 腐蝕動(dòng)力學(xué)
材料被強(qiáng)腐蝕性高溫堿金屬氯鹽腐蝕后從表至里可分成四層,分別為腐蝕外層、腐蝕次外層、腐蝕內(nèi)層和基體層,其中完全暴露于鹽中的腐蝕外層和次外層是高溫鹽與保護(hù)性氧化膜的反應(yīng)產(chǎn)物[9].由圖1(a)可知,在600 ℃的不同混合鹽中腐蝕12h后,試樣的質(zhì)量均明顯大于腐蝕前的,此時(shí)測得的腐蝕產(chǎn)物厚度為腐蝕外層厚度.在30%NaClG70%KCl
混合鹽中腐蝕12h后,試樣的質(zhì)量增加量約為在其他兩種混合鹽中的2倍.隨著腐蝕時(shí)間的延長(24~60h),試樣的外層腐蝕產(chǎn)物逐漸脫落,造成試樣質(zhì)量的快 速 減 少.腐 蝕 60h 后,試 樣 在 70%NaClG30%KCl混合鹽中的單位面積質(zhì)量損失約為5mg??m-2,在50%NaClG50%KCl混合鹽中的約為5.9mg??m-2,而在30%NaClG70%KCl混合鹽中的最大,達(dá)到10.5mg??m-2,可見高溫混合鹽中 KCl含量的增加會(huì)加快腐蝕產(chǎn)物的脫落.由圖1(b)可知,隨著腐蝕時(shí)間的延長或混合鹽中 KCl含量的增加,未脫落腐蝕產(chǎn)物的厚度增大.在腐蝕過程中,外層腐蝕產(chǎn)物不斷脫落,次外層則不斷變?yōu)楦g外層.結(jié)合圖1(a)與圖1(b)可知,隨著脫落的腐蝕產(chǎn)物質(zhì)量的增加(即由于產(chǎn)物脫落而導(dǎo)致的試樣腐蝕質(zhì)量損失的增大),相應(yīng)未脫落部分腐蝕產(chǎn)物的厚度也增大.說明隨著混合鹽中 KCl含量的增加,12Cr1MoV 鋼表面腐蝕產(chǎn)物的總厚度將增大.
2.2 表面腐蝕形貌及化學(xué)成分
由圖2可知,在700 ℃、70%NaClG30%KCl混合鹽中腐蝕60h后,試樣表面發(fā)生了較明顯的沿晶腐蝕;腐蝕產(chǎn)物結(jié)構(gòu)較為致密且晶界處被大量的顆粒狀腐蝕產(chǎn)物所覆蓋,顆粒狀腐蝕產(chǎn)物較為圓整;而在30%NaClG70%KCl混合鹽中腐蝕后,試樣表面產(chǎn)物較疏松,偏向于整體性的侵蝕;腐蝕產(chǎn)物呈疏松的無規(guī)則長條絮狀結(jié)構(gòu),且可在產(chǎn)物上觀察到大量
的孔洞.由此可見,高溫堿金屬鹽中 NaCl和 KCl的配比對(duì)試樣表面的腐蝕產(chǎn)物有很大的影響.在高溫?zé)釕?yīng)力的作用下,孔洞處容易產(chǎn)生應(yīng)力集中,造成腐蝕裂紋的萌生及失穩(wěn)擴(kuò)展.
由圖3可以看出,在700 ℃混合鹽中腐蝕60h后,試樣表 面 的 腐 蝕 產(chǎn) 物 都 含 有 大 量 的 鐵、氧、碳元素,且在30%NaClG70%KCl混合鹽中腐蝕后表面的氧 元 素 含 量 明 顯 高 于 在 70%NaClG30%KCl混合鹽中腐蝕的.可見試樣均發(fā)生了嚴(yán)重的氧化腐蝕,且在30%NaClG70%KCl混合鹽中的腐蝕程度更嚴(yán)重.
2.3 截面腐蝕形貌及化學(xué)成分
由圖4和表2可見,分別在600 ℃,70%NaClG30%KCl和30%NaClG70%KCl混合鹽中腐蝕60h后,試樣的平均腐蝕內(nèi)層厚度分別約為80,700μm,可見經(jīng)較多 KCl含量混合鹽腐蝕后的腐蝕層厚度較大,腐蝕程度加深,與圖1分析結(jié)果一致.在腐蝕區(qū)域均檢測到鐵、氧、鉻、氯、硅等元素.在30%NaClG
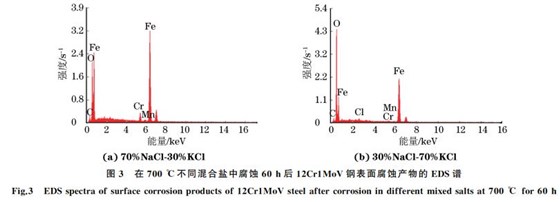
70%KCl混 合 鹽 中 腐 蝕 后,試 樣 的 腐 蝕 層 比 在70%NaClG30%KCl混合 鹽 中 腐 蝕 后 的 疏 松,可 觀察到大 小 不 一 的 孔 洞 缺 陷. 當(dāng) 溫 度 升 至 700 ℃時(shí),經(jīng)70%NaClG30%KCl混 合 鹽 腐 蝕 后,試 樣 的平均腐蝕內(nèi)層厚度到100μm 左右,與600 ℃時(shí)的相比厚度增大且腐蝕層中產(chǎn)生大量的縱向裂紋;經(jīng)30%NaClG70%KCl混合鹽腐蝕后,平均腐蝕內(nèi)層厚度則約為800μm,與在600 ℃時(shí)的相比,該腐蝕層孔洞數(shù)量多,厚度明顯增大.由此可見,較高溫度的堿金屬氯鹽對(duì)試樣的腐蝕更劇烈.由表2還可以看出,氯元素主要分布于腐蝕層靠外側(cè)區(qū)域,而靠基體一側(cè)區(qū)域因腐蝕反應(yīng)形成孔洞的尺寸與數(shù)量明顯小于腐蝕層靠外側(cè)區(qū)域的,說明除溫度以外,堿金屬氯鹽的腐蝕強(qiáng)度同樣可影響孔洞尺寸.
NaCl的高,KCl也 就 更 易 與 金 屬 材 料 接 觸 而 發(fā) 生反應(yīng).同時(shí),由于 KCl、NaCl與金屬及金屬氧化物的反應(yīng)產(chǎn)物 的 熔 點(diǎn) 不 同,使 得 腐 蝕 機(jī) 制 有 很 大 的區(qū)別.KCl與金屬氧化物形成的共晶化合物熔點(diǎn)一般在202~220 ℃ 之 間,普 遍 低 于 NaCl與 金 屬氧化物反應(yīng) 得 到 的 共 晶 化 合 物 的 熔 點(diǎn),這 些 化 合物在高溫 下 更 易 呈 液 相 熔 池 狀,對(duì) 12Cr1MoV 鋼的腐蝕影 響 比 由 NaCl與 金 屬 氧 化 物 反 應(yīng) 形 成 的化合物的要高得多.
2.4 腐蝕機(jī)制
由圖6可知,在700 ℃、30%NaClG70%KCl混合鹽中腐蝕后,試樣的腐蝕外層中只存在鐵和氧元素;從腐蝕次外層到內(nèi)層,均檢測到了一些其他的元素;在腐蝕外層和次外層中均不存在鉻和硅元素,可見在試驗(yàn)初期形成的具有保護(hù)性的Cr2O3 及SiO2 氧化物層被高溫氯鹽腐蝕所破壞,且在熱腐蝕環(huán)境中這些保護(hù)層不能再次形成[9].氯元素存在于腐蝕次外層與內(nèi)層中,且內(nèi)層中的含量約為次外層中的2倍.
從 截 面 形 貌 與 元 素 變 化 規(guī) 律 并 根 據(jù) 相 關(guān) 文獻(xiàn)[10]可知,合金鋼在高溫氯鹽混合物中的腐蝕機(jī)制為氯元素的活化氧化行為.Antunes等[4]指出誘發(fā)活化氧化的主要原因是材料表面的氧化膜被熱腐蝕破壞.當(dāng)表面失去保護(hù)作用時(shí),氯鹽便會(huì)加速材料的腐蝕氧化速率.腐蝕過程的化學(xué)反應(yīng)如式(1)~(5)(M=Na,K)所示.
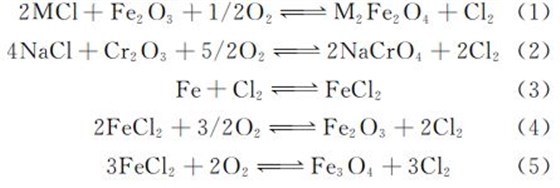
由式(1)~ (5)可知,在反應(yīng)初期,高溫氯鹽與試驗(yàn)鋼中的金屬氧化物相互作用產(chǎn)生 Cl2,Cl2 會(huì)通過表面微 小 的 孔 洞 和 裂 紋 進(jìn) 入 內(nèi) 部,并 反 應(yīng) 生 成FeCl2.此時(shí)的 FeCl2 極不穩(wěn)定,易在高溫下由固態(tài)轉(zhuǎn)變?yōu)闅鈶B(tài).當(dāng)氣態(tài)的 FeCl2 通過試驗(yàn)鋼內(nèi)部的缺陷結(jié)構(gòu)進(jìn)入到氧分壓較高處時(shí)會(huì)被氧化成為 Fe2O3和 Fe3O4 并再次釋放出 Cl2,這也是在腐蝕外層中
無法檢測到氯元素的原因.在此過程產(chǎn)生的 Cl2 向外擴(kuò)散,沖破了金屬表層與基體之間的氧化層,導(dǎo)致在腐蝕內(nèi)層形成大小不一的孔洞.根據(jù)文獻(xiàn)[11]可知,NaCl含量較高時(shí),反應(yīng)中形成的 Cl2 會(huì)在強(qiáng)度較低的晶界處形成微小的孔洞.因此,晶界裂紋是由于大量微孔洞擴(kuò)展而產(chǎn)生的.而隨著混合鹽中KCl含量的升高,腐蝕作用增強(qiáng),導(dǎo)致 Cl2 不只在晶界上產(chǎn)生缺陷,其影響范圍也會(huì)擴(kuò)大到內(nèi)部.由于腐蝕次外層與內(nèi)層氧分壓相對(duì)較低,FeCl2 未被完全氧化,因此氯元素可被檢測到,且腐蝕內(nèi)層相對(duì)于腐蝕次外層的氧含量更低,導(dǎo)致該層中氯元素的含量更大.新生成的氧化物的生長會(huì)導(dǎo)致較大的組織應(yīng)力,使氧化膜的完整性遭到破壞,導(dǎo)致氧化膜鼓泡、隆起、破裂.在這個(gè)過程中,不斷形成的外層腐蝕產(chǎn)物與基體發(fā)生分離[12-13],從而導(dǎo)致鋼試樣的質(zhì)量迅速減輕.
3 結(jié) 論
(1)12Cr1MoV 鋼在高溫混堿金屬合氯鹽中會(huì)發(fā)生嚴(yán)重的表面與內(nèi)部腐蝕,其內(nèi)部產(chǎn)生的 Cl2 是導(dǎo)致裂紋與孔洞等缺陷萌生和擴(kuò)展的主要原因.
(2)NaClGKCl混合鹽中 KCl含量的增多和溫度的升高會(huì)增大12Cr1MoV 鋼的腐蝕速率;在腐蝕12h時(shí),試樣質(zhì)量增加,隨著腐蝕時(shí)間的延長,腐蝕產(chǎn)物與基體分離,試樣的質(zhì)量快速減少.
(3)NaClGKCl混 合 鹽 中 KCl含 量 的 升 高 使12Cr1MoV 鋼的表面腐蝕產(chǎn)物由圓整顆粒狀向疏松絮狀轉(zhuǎn)變;其腐蝕機(jī)制也由沿晶腐蝕轉(zhuǎn)變?yōu)閮?nèi)部的整體性侵蝕.
(4)隨著溫度的升高,12Cr1MoV 鋼內(nèi)部所產(chǎn)生的裂紋、孔洞的數(shù)量與尺寸均明顯增大;影響缺陷尺寸的另一個(gè)重要因素則為高溫氯鹽的腐蝕強(qiáng)度.
(文章來源:材料與測試網(wǎng)-機(jī)械工程材料)